
The lithium anode and the catholyte were separated by a water-stable NASICON-type lithium-ion conducting solid electrolyte. Wu and colleagues reported a lithium battery using an aqueous electrolyte solution with a lithium anode and a LiFePO 4 ( Hou et al., 2013 Chang et al., 2016), LiCoO 2 ( Wang et al., 2013b), or LiMn 2O 4 ( Wang et al., 2013a) cathode. Goodenough and colleagues ( Lu et al., 2011) proposed an aqueous lithium battery with a lithium anode and an aqueous Fe(CN) 6 3–/Fe(CN) 6 4– redox couple, and Imanishi and colleagues ( Morita et al., 2017, 2018 Watanabe et al., 2019) proposed an aqueous lithium battery with a lithium anode and an aqueous MCl 2/M (M = Sn, Co, and Ni) redox couple. Some other types of lithium aqueous batteries with a similar water-stable lithium-ion-conducting solid electrolyte were also proposed by many groups. The aqueous lithium-air battery consists of a lithium anode, a lithium-stable interlayer electrolyte, a water-stable lithium conducting solid electrolyte separator, an aqueous catholyte, and an air electrode. As the cell reaction product in this system is soluble in the catholyte, a high-power-density aqueous lithium-air batteries were reported ( Imanishi and Yamamoto, 2019). The aqueous system with an acidic catholyte does not require a water purification system ( Zhang et al., 2010 Soga et al., 2020). The theoretical energy densities of the aqueous lithium-air battery are 1,910 W h kg –1 and 2,004 W h L –1, which are lower than those of non-aqueous lithium-air batteries but five and two times higher than those of the conventional lithium-ion batteries in terms of mass and volume, respectively ( Yamamoto, 2014). The aqueous lithium-air battery is one attractive candidate for application as the power source in electric vehicles because of its high energy and power densities.
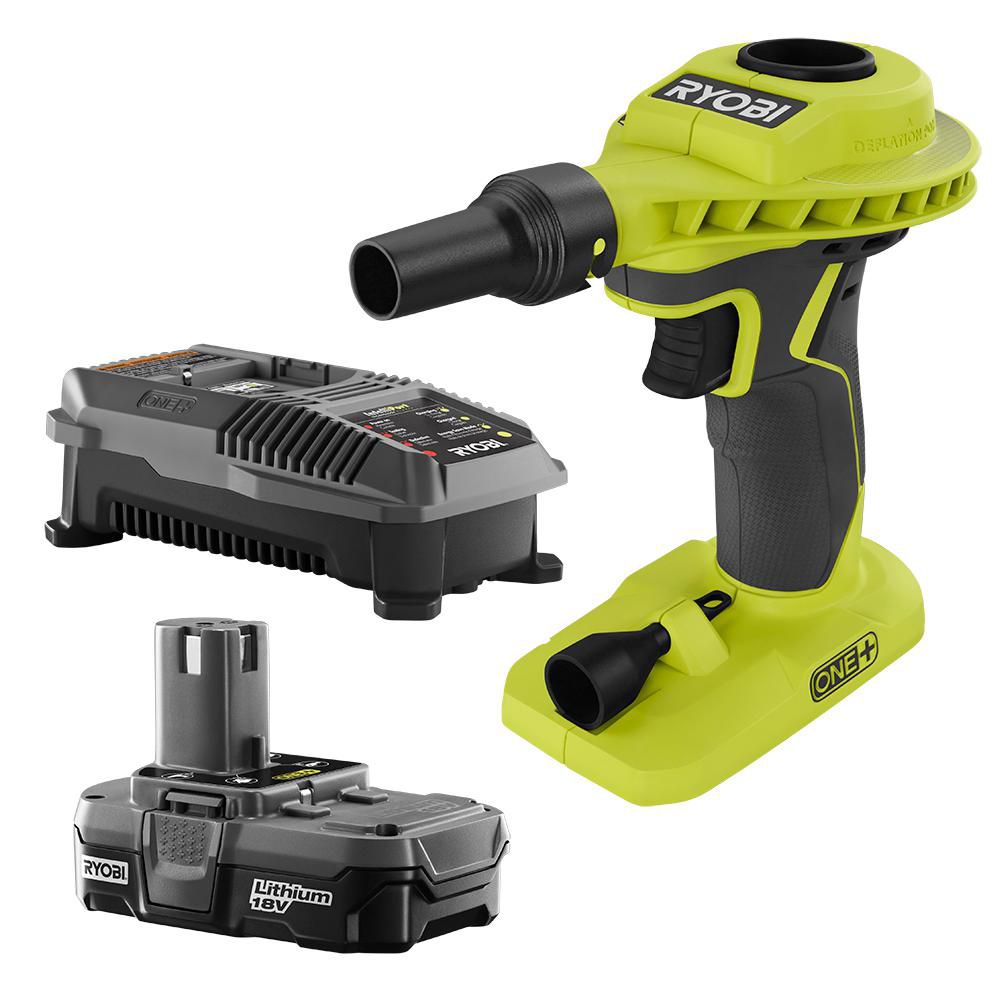
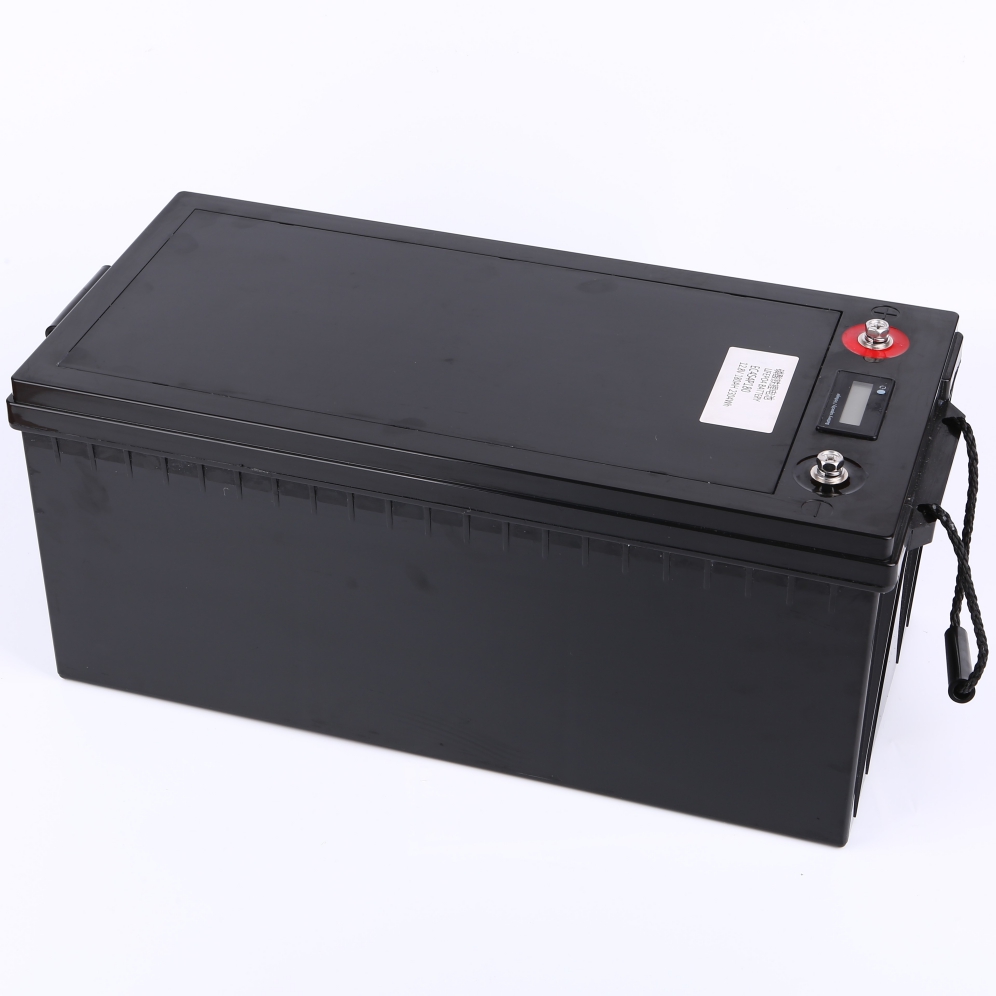
All-solid-state batteries have inherent safety, a wide operable temperature range, and potential benefits in terms of the power density however, the estimated specific energy density is only slightly higher than that of the conventional lithium-ion battery ( Kato et al., 2016). The lithium–sulfur system, which has high specific energy densities of 2,567 W h kg –1 and 2,199 W h L –1, has a serious problem of dissolution of the reaction product into the electrolyte ( Bruce et al., 2012). The non-aqueous lithium-air system has the highest theoretical specific energy density, which is as high as 3,505 W h kg –1 and 3,436 W h L –1 however, this system requires an air purification system or oxygen tank ( Gallagher et al., 2014). Several types of high-energy-density batteries, such as lithium–sulfur ( Yamin et al., 1988 Shim et al., 2002), non-aqueous lithium-air ( Abraham and Jiang, 1996 Lu et al., 2014 Gao et al., 2017), aqueous lithium-air ( Visco et al., 2004 Zhang et al., 2010), and all-solid-state ( Takada, 2013 Kato et al., 2016) batteries have been extensively studied in the last few decades. The aqueous lithium-air battery with the solid electrolyte separator was successfully cycled at 0.5 mA cm –2 and 25☌ in an air atmosphere. In this work, we have developed a water-stable and water-impermeable solid electrolyte with a high lithium-ion conductivity of around 10 –3 S cm –1 at room temperature by the addition of epoxy resin and LiCl into a tape-cast NASICON-type Li 1. A key component of this system is the water-stable lithium-ion-conducting solid electrolyte. The theoretical energy density of this system is 1,910 W h kg –1, which is around five times higher than that of conventional lithium-ion batteries. The battery system consists of a lithium anode and an aqueous solution catholyte, which are separated by a water-stable lithium-ion-conducting solid electrolyte, and an air electrode.

4Automobile Electrical Design Department, Suzuki Motor Corporation, Hamamatsu, JapanĪqueous lithium-air batteries are one of the most promising batteries for electric vehicles because of its high energy and power density.3Department of Physics, Faculty of Engineering, Jiangsu University, Zhenjiang, China.2Graduate School of Engineering, Mie University, Tsu, Japan.1The State Key Laboratory of High Performance Ceramics and Superfine Microstructure, Shanghai Institute of Ceramics, Chines Academy of Science, Shanghai, China.

Fan Bai 1,2, Kouichi Kakimoto 2, Xuefu Shang 3, Daisuke Mori 2, Sou Taminato 2, Mitsuhiro Matsumoto 2, Yasuo Takeda 2, Osamu Yamamoto 2*, Hiroaki Izumi 4*, Hironari Minami 4 and Nobuyuki Imanishi 2
